Active lime production line
Key words:
Active lime production line
Classification:
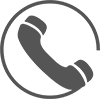
Hotline:
Active lime production line
Product introduction:
Our company can provide complete sets of equipment and one-stop service for the active lime production line with a daily output of less than 1200 tons.
Active lime is widely used in steel, alumina, magnesium metal, calcium carbide and power plant desulfurization paper industry. Active lime is an important auxiliary raw material for steelmaking, and the use of active lime has a series of characteristics such as improving the quality of molten steel, increasing production, reducing steelmaking consumption and cost, and stabilizing operation. Practice has proved that all enterprises that use active lime in steelmaking have achieved remarkable economic benefits. In the past ten years, the output of lime for steelmaking in China has increased by 40%, but the high-grade lime with an activity of more than 300ml has increased from 27% to 29.5 of the total steelmaking lime, an increase of only 2.5.
Technical parameters:
Process flow of active lime system
Qualified limestone is stored in the silo, lifted by the hoist and transported into the silo at the top of the preheater. At the top silo of the preheater, the feeding amount is controlled by two upper and lower level gauges, and then the limestone is evenly distributed to each chamber of the preheater through the discharge pipe. Limestone is heated to about 900°C by kiln flue gas at 1150°C in the preheater, and about 30% is decomposed. It is pushed into the rotary kiln through a hydraulic push rod. Limestone is sintered and decomposed into CaO and CO in the rotary kiln.2. The limestone generated after decomposition enters the cooler, and is cooled to 100°C by the cold air blown in the cooler and discharged. The heat-exchanged 600°C hot air enters the kiln and is mixed with the gas for combustion. The exhaust gas is mixed with cold air into the bag filter through the induced draft fan, and then into the chimney through the exhaust fan. The lime from the cooler is sent to the lime finished product warehouse by vibrating feeder, chain bucket conveyor, bucket elevator and belt conveyor. According to customer requirements whether screening and other processes.
Lime Rotary Kiln Series Host Equipment Configuration
scale of production |
600t/d |
800t/d |
850t/d |
1000t/d |
1200t/d |
|
preheater |
Specifications |
12-Push Head |
12-Push Head |
14-Push Head |
18-Push Head |
20-Push Head |
Number of preheating boxes |
12 |
12 |
12 |
18 |
20 |
|
Number of hydraulic push rod |
12 |
12 |
12 |
18 |
20 |
|
Preheat (ton) |
1200 |
1600 |
1600 |
2000 |
2400 |
|
rotary kiln |
Model |
Φ4 × 60m |
Φ4.3 × 62m |
Φ4.5 × 68m |
Φ4.9 × 72m |
Φ5.1 × 78m |
Slant |
3.5% |
3.5% |
3.5% |
3.5% |
3.5% |
|
Revolutions (r/min) |
0.3-1.8 |
0.3-1.8 |
0.3-1.8 |
0.3-1.8 |
0.3-1.8 |
|
Preheating temperature (℃) |
1350 |
1350 |
1350 |
1350 |
1350 |
|
Vertical cooler |
Number of temperature control zones |
3 |
4 |
4 |
4 |
4 |
Tower quantity |
4 1 |
4 1 |
4 1 |
4 1 |
4 1 |
|
Specification (m) |
4.1 × 4.1 |
4.7 × 4.7 |
4.7 × 4.7 |
5.2 × 5.2 |
5.4 × 5.4 |
|
discharge temperature (℃) |
≤ 80 |
≤ 80 |
≤ 80 |
≤ 80 |
≤ 80 |
|
Product heat consumption |
5400 |
5000 |
5000 |
4750 |
4600 |
Previous Page
None
Next Page